- 放大
- 缩小
- 默认
航煤管输溯源质量管理的探讨
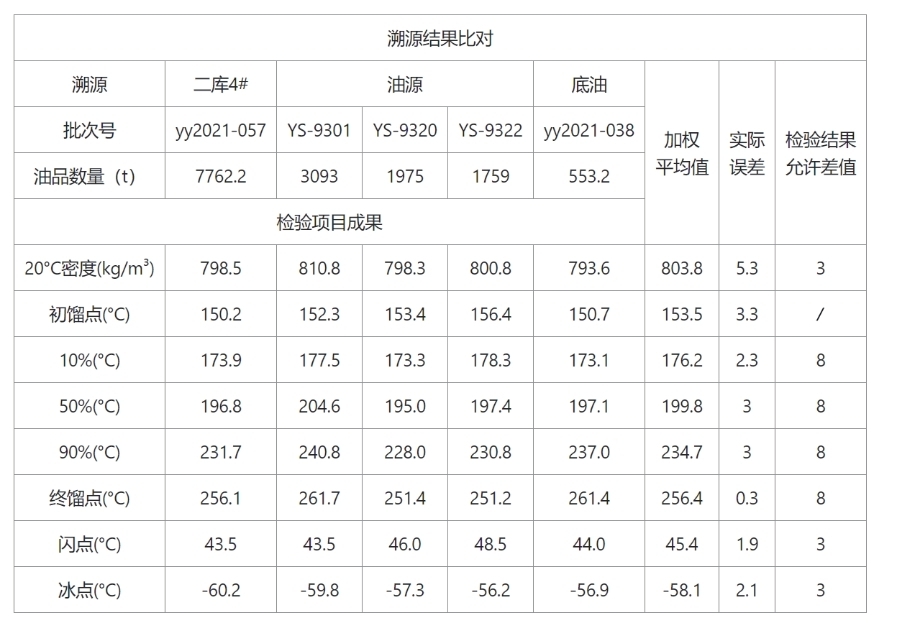
图5 溯源结果比对
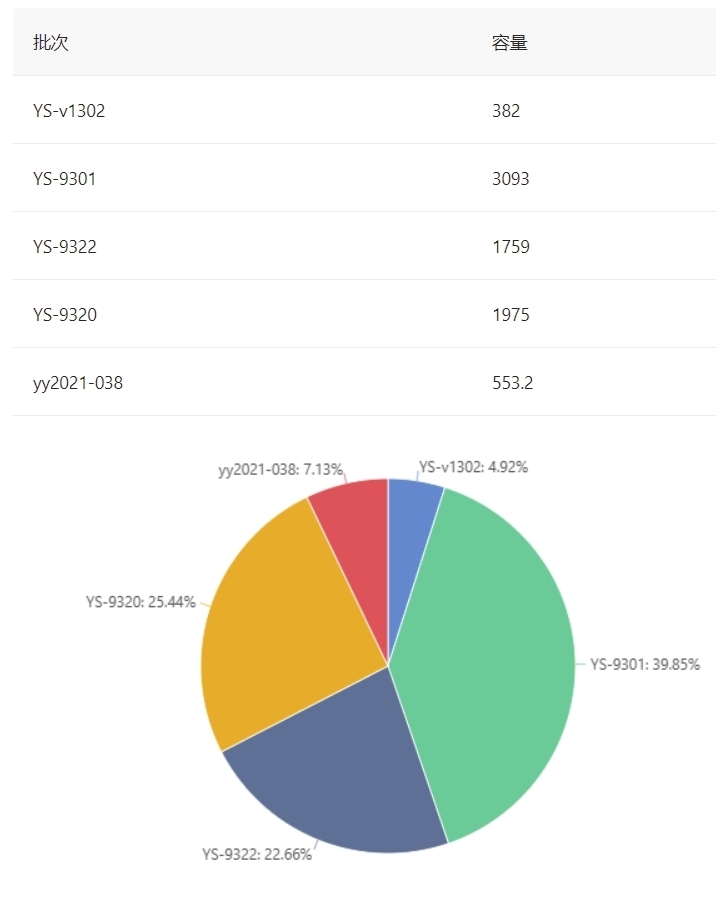
图6 各批次油品在储油罐中的占比
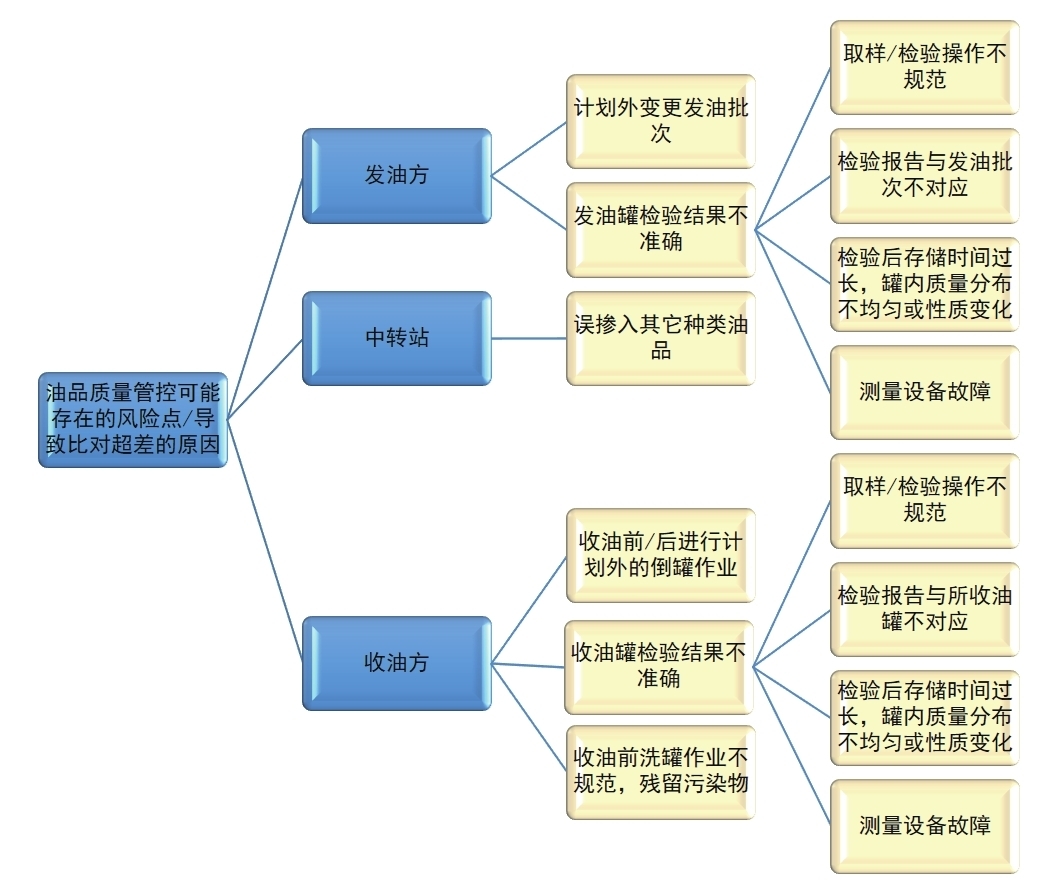
图7 质量管理各环节中可能存在的问题来源
如图5所示,针对某一储罐,例如二库4#储油罐,软件可以根据所存油品的各批次来源进行参数汇总与比对。通过输入各批次油品的检验结果,结合各批油品在存油中的占比(如图6所示),可以计算得到油品各项参数的加权平均值。将所得的数值与对存油取样化验得到的数值进行比对,分析各项检验结果的计算值与实测值的差值,与允许差值对比。若计算所得差值超过了允许差值,则溯源及质量比对的过程反映出油品质量管控的某个环节存在问题。
基于溯源的质量风险分析与管控方法
之前的油品质量分析过程仅仅分析油品质量各参数是否合格,无法对质量管控各环节的操作实施监管,出现质量问题也无法分析问题的来源或采取有针对性的措施。而基于溯源的质量风险分析与管控则能借助统计学、信息技术的手段,帮助管理人员排查质量管控各环节中的可能存在的风险点,排查隐患,找准问题的源头,及时发现和纠正错误,在此基础上进一步规范操作流程、对各环节实现实时监控与监督,通过系统对可能的错误操作带来的风险实施有效管控,通过发现问题、找准源头、优化管控规避风险的“三步法”,从源头上预防涉及油品质量问题的隐患和事故。
依据统计学的原理,利用软件比对的手段,可能发现从发油方发出到收油方接收的过程中存在油品质量管控的问题。如图7所示,若比对结果超过允许差值,有多种可能的原因,需要对具体问题进行分析,可以对照此图开展风险排查,找出原因所在。
针对收油方油品质量检验环节,超差也许反映下游的质量检验机构所取样品存在问题,样品可能没有正确反映整个储罐存油整体的性质,不具代表性。首先,这可能是由于罐内油品本身有分层或者罐内各位置油品的质量不均匀,体现在油罐不同位置所取样品的性质差异明显。其次,取样操作中也可能存在问题。如果操作人员没有按操作规程在各不同液位高度多次取样,而是在同一液位多次取样,将导致样品无法合理反映全罐油品的整体特性,而取样过