- 放大
- 缩小
- 默认
航煤管输溯源质量管理的探讨
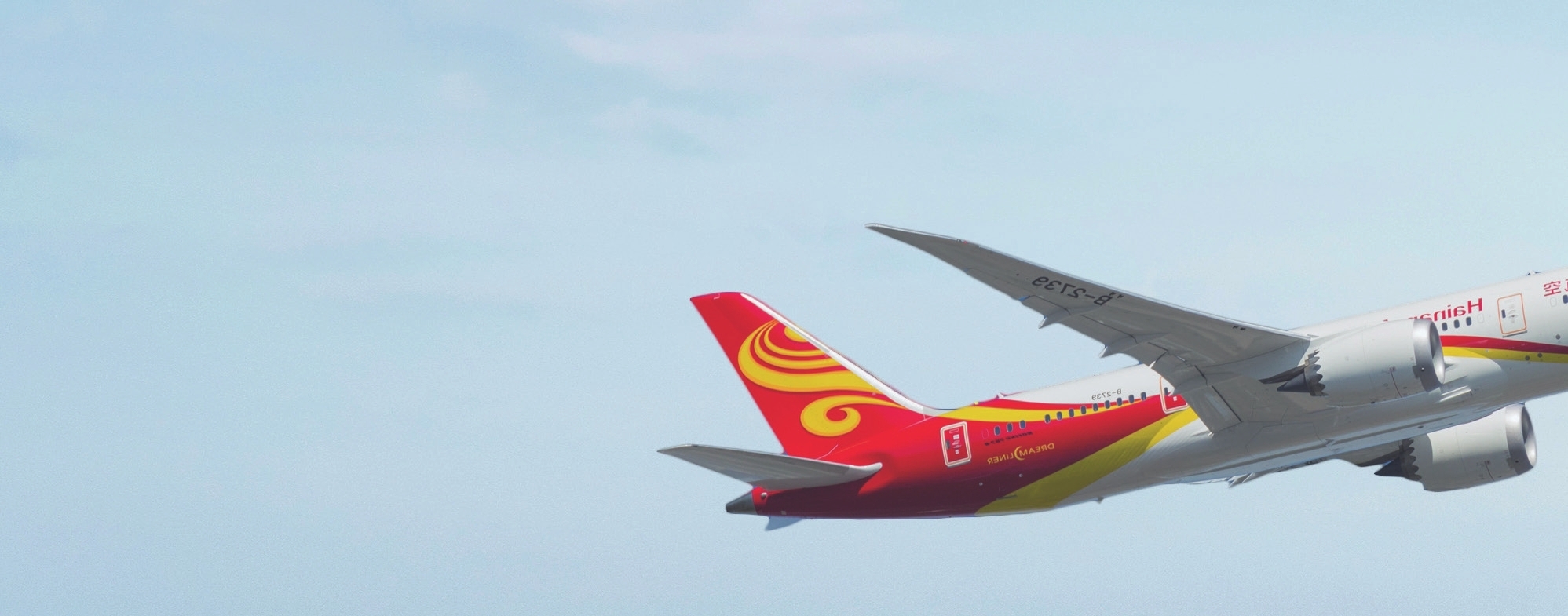
程操作不当或使用不合格工器具也可能引入杂质或者对结果产生干扰。另外,比对超差也可能反映测量参数的仪器本身存在问题。
航煤在经过长输管道输送的过程中,意外情况下,误操作或某些设备故障可能导致所输航煤与其他种类油品混合,使油品性质发生变化。溯源及油品质量比对也可能反映此类问题。
针对下游收油油库各项作业,若收油作业前进行了洗罐作业,或在收油前后实施倒油进罐作业,则洗罐后在罐内残留的杂质或倒罐倒入的油品可能对后续所存油品的性质产生影响。若倒罐作业情况没有及时、准确地录入溯源系统,也可能导致软件计算比对结果超差。
除此之外,结果比对也可能反映上游炼厂所提供的产品合格证与所发油品批次不一致,或者发油方的取样化验过程中存在问题。针对航煤输送与储存过程中的质量管控。所有上述因素均可能导致最终的比对结果不合格,在发现问题后须对相关数据信息进行分析,开展风险排查,找准问题源头才能有针对性地解决。
质量管控问题排查与解决案例
自投入运行4个月以来,该系统的实际运行结果显示,出现了3次超差。下面具体阐述分析超差原因的几个过程,可以帮助说明实际应用中该系统如何定位油品质量管控中的问题,从而有助于管控过程的精细化和规范化。例如图5所示“20℃密度项”的一次超差,实际误差5.3千克/立方米超过了检验结果允许差值。具体分析比对的过程,实际测量4#罐油样密度为798.5千克/立方米,油源与底油的加权平均值803.8千克/立方米较测量值偏高。分析构成加权平均值的基础数据,底油密度793.6千克/立方米、YS-9320批次油品的密度798.3千克/立方米均低于4#罐油样密度测量值,YS-9322批次油品的密度800.8千克/立方米也低于加权平均值。所以,加权平均值偏高源于YS-9301批次油品的密度值偏高,初步判断该数值可能存在问题。进一步检查化验报告,可以发现YS-9301批次油品的质量检验结果是在发油前25天检验所得到。此外,由于发油方油罐管容较大,一批次油品发到二库时由多个收油罐接收,在二库经历了多次化验,同一YS-9301批次油品收到二库时的各次化验结果并不一致。这一事实说明,由于存储时间较长,实际向二库发油时油品已经分层,发出的同一批次油品的密度参数会偏离原结果。据推测,这可能是由于疫情影响,航班加油量偏少,导致油库周转频次减少,中转油库油品发出前的存储时间变长。从质量管理精细化的角度出发,如果存储时间较长,为了确保质量管控可靠,建议发油方在发油前再做化验,确保检验所得的结果能够切实反映发出油品的质量情况。若发现油品分层,应及时打循环确保整罐油品质量分布均匀。
实际运行中也曾发现其他造成超差的原因。例如,某次收油中,收油方使用该系统分析发现,油罐检验结果与各油源加权平均值的偏差超过允许值;联系发油方确认质量报告上的参数,发现发油方值班员交接不清,没有按计划发油,而计划外的油源数据并未提供给收油方;后续,在该系统中更新相关数据、重新计算后,修正后的误差处于合理范围内。在另一次超差问题中,收油罐实测油样与各油源、底油比对,各参数均超差,观察发现实测收油罐油样与底油的各参数非常接近,两者密度均明显小于油源来油的密度,反映出给收油罐取样时所取油样不具代表性,可能只取了上层油样,所得结果不能正确反映全罐油品的质量情况;后续,通过规范取样操作、对收油罐重新取样检验,用所得数据重新计算误差,发现纠正后的误差在允许范围内。